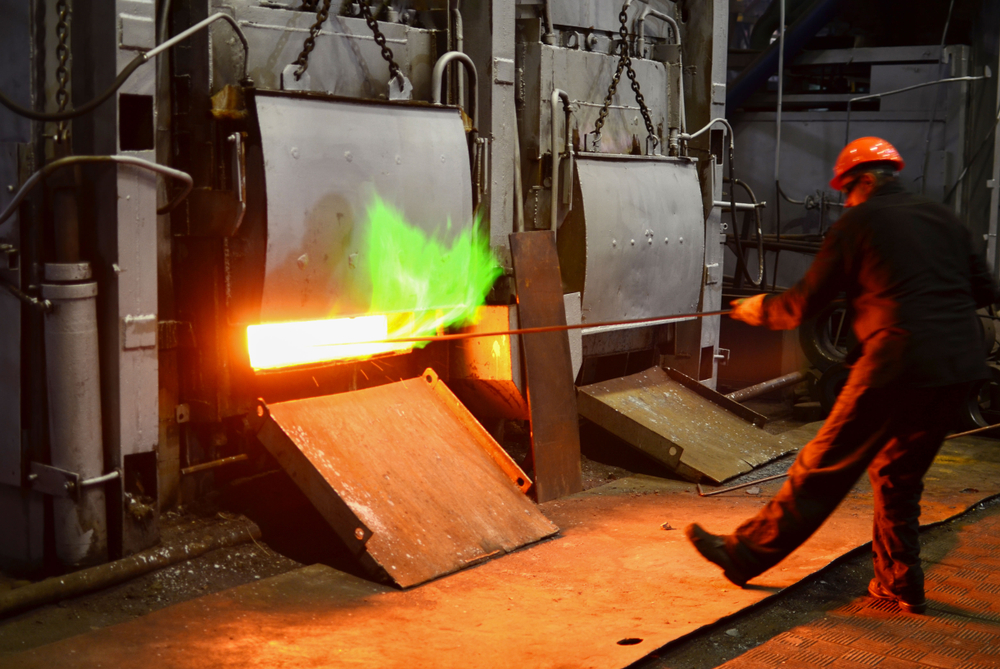
Heat treatment processes are essential to modify the properties of metals to meet specific performance standards. Among the many heat treatment techniques available, two of the most commonly used are annealing and quenching. Both annealing and quenching involve controlled heating and cooling of metal alloys, but they achieve different results. If you’re working with metal components, understanding the distinctions between these processes is crucial for selecting the right technique for your project. In this blog, we’ll compare annealing and quenching, highlighting the differences, advantages, and applications of each process, so you can determine which one best suits your needs.
Understanding the Annealing Process
Annealing is a heat treatment process that involves heating a metal to a specific temperature, holding it at that temperature for a set period, and then allowing it to cool slowly, often in air or in a furnace. The primary purpose of annealing is to reduce the hardness of a material, making it more ductile and easier to work with. This process helps relieve internal stresses that may have been introduced during earlier stages of metal processing, such as cold working or welding.
In the annealing process, metals like steel, copper, aluminum, and other alloys undergo a transformation in their microstructure. The heating phase allows the metal to reach a temperature where the crystalline structure changes, making it more uniform. As the metal cools gradually, its atoms rearrange to form a more stable structure. This results in improved material properties like enhanced formability, reduced brittleness, and increased toughness.
Annealing is particularly beneficial when working with metals that need to be easily shaped or formed. It softens the material, allowing for machining, welding, or further processing without causing damage to the metal. Industries such as automotive, aerospace, and manufacturing often use annealing services in Gastonia, NC, to enhance the quality of their metal products.
The Quenching Process and Its Benefits
Quenching, on the other hand, is a heat treatment process designed to increase the hardness and strength of metals, particularly steel and other high-carbon alloys. The process involves heating the metal to a high temperature, followed by rapid cooling, typically by immersion in water, oil, or air. The goal of quenching is to harden the material, making it more resistant to wear and tear, as well as improving its tensile strength.
When a metal is heated to a specific temperature, its crystal structure becomes more disordered, and the material can undergo phase transformations. By rapidly cooling the metal, the atoms in the metal have less time to rearrange, resulting in a harder and more brittle material. The rapid cooling “locks” the metal’s microstructure in a high-energy state, which increases its hardness.
While quenching makes the material stronger, it also makes it more brittle. This is why quenching is often followed by a tempering process. Tempering involves reheating the metal to a lower temperature to reduce brittleness while maintaining the hardness gained during quenching. Metal quenching is commonly used in manufacturing processes where high strength and durability are necessary, such as the production of tools, gears, and engine components.
Key Differences Between Annealing and Quenching
Although both annealing and quenching involve heating metals to a specific temperature, the cooling rates and the results of each process differ significantly. Annealing focuses on making the metal softer and more ductile, while quenching aims to increase the hardness and strength of the material. The cooling rate is one of the most significant differences between the two processes.
Annealing involves a slow, controlled cooling process, which allows the metal to retain a more uniform, stable crystalline structure. Slow cooling prevents the formation of unwanted internal stresses and reduces the risk of cracking. This gradual cooling makes the metal more malleable and less prone to breaking under stress.
In contrast, quenching involves rapid cooling, which leads to the formation of a more brittle microstructure. While this increases the hardness of the material, it also makes it less flexible. The rapid cooling process can introduce internal stresses, which is why it is often followed by tempering to alleviate some of the brittleness while maintaining the hardness achieved through quenching.
Another notable difference is the temperature range used in each process. Annealing typically involves heating the metal to a temperature below its melting point, while quenching requires heating the metal to a much higher temperature, often just below its melting point. This higher temperature is necessary for quenching to induce phase changes and harden the material effectively.
Applications of Annealing and Quenching
Both annealing and quenching have broad applications across various industries, but each process is suited for different purposes depending on the desired material properties.
Annealing is ideal for projects that require improved workability, such as bending, shaping, or machining. For example, softening metal for subsequent forging or machining can be easily achieved through annealing. It is commonly used in the production of metal sheets, wires, and pipes, where the metal must retain good ductility to be processed further. Annealing is also used in the manufacturing of products where enhanced toughness and resistance to cracking are critical. For industries in Gastonia, NC, and elsewhere, annealing services are often used to improve the quality of metal parts that need to be manipulated or welded without fracturing.
On the other hand, quenching is primarily used when high hardness and wear resistance are essential. It is a standard technique in the production of cutting tools, gears, bearings, and other components that must withstand high levels of mechanical stress. The aerospace, automotive, and manufacturing sectors often employ quenching to create metal parts that must endure extreme conditions. Whether it’s the durability of engine components or the precision required in machine tools, quenching helps to deliver the necessary strength and resistance to wear.
In many cases, quenching is not performed in isolation but is part of a larger heat treatment cycle. After quenching, tempering is used to reduce the brittleness of the material while retaining much of the hardness. This combination of quenching and tempering is particularly common in toolmaking, where a balance between hardness and toughness is critical.
Choosing the Right Heat Treatment for Your Project
When deciding between annealing and quenching for your project, it’s important to consider the specific requirements of the final product. If your goal is to soften the metal, relieve internal stresses, and enhance ductility for easier processing or forming, then annealing is likely the right choice. If you need to increase the strength, hardness, and wear resistance of the material, then quenching may be more appropriate.
It’s also essential to consider the material you’re working with. Different alloys respond to heat treatment processes in different ways, and the ideal technique can vary depending on the metal’s composition. For example, quenching is particularly effective for high-carbon steels, which respond well to rapid cooling, while annealing is more suited for materials like copper and aluminum that benefit from slower cooling to improve their properties.
Both processes require specialized knowledge and equipment to ensure that the desired properties are achieved without compromising the material’s integrity. For businesses in Gastonia, NC, seeking expert annealing services or metal quenching, it is important to consult with experienced professionals who can guide you through the decision-making process and help you choose the best heat treatment method for your needs.
In conclusion, whether you need the softness and ductility offered by annealing or the hardness and strength achieved through quenching, both heat treatment processes have distinct advantages. By understanding the differences between these two techniques, you can make an informed decision that will result in the optimal performance and durability of your metal components.
Need Heat Treatment Services in Gastonia, NC?
Family owned and operated J.F. Heat Treating Inc, is a metal heat treating service company with more than 34 years of experience! Heat treatment is the controlled heating and cooling of metals to alter their physical and mechanical properties without changing the product shape. We specialize in the through hardening and carbonizing of various steel products in a metallurgical lab. It is our privilege to service and work with the manufacturing and fabrication industries to give the best product service available! Our heat treating services include annealing, aging, quenching and tempering to soften, harden, stress relieve, remove contaminants or provide other material characteristics to parts and components. Contact us today to learn more about what we can do for you!