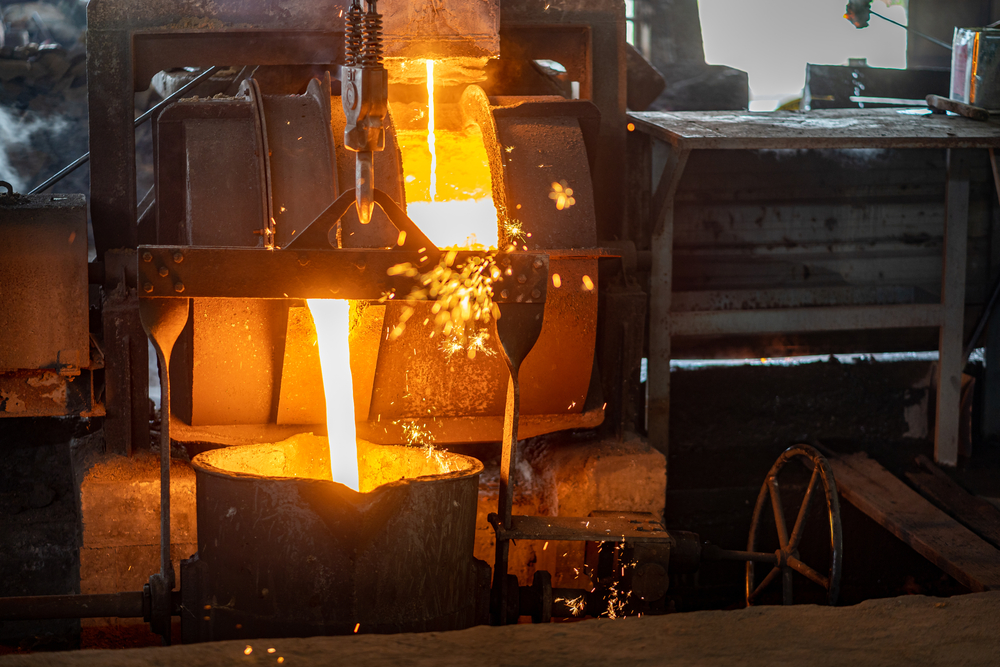
Metal plays a critical role in countless industries, from construction and manufacturing to aerospace and automotive. Yet, the effectiveness of metal in these applications depends heavily on its durability and performance. This is where the heat treating process comes into play, offering a transformative solution to enhance metal’s properties. Below, we delve into how heat treating improves metal durability and performance, ensuring materials can withstand the most demanding environments.
Understanding the Heat Treating Process
Heat treating is a controlled process used to alter the physical and chemical properties of metal. By carefully applying heat and cooling, metallurgists can manipulate metal’s structure, resulting in enhanced characteristics such as strength, toughness, and hardness. The process is highly versatile, suitable for a variety of metals including steel, aluminum, and titanium.
Key Steps in the Heat Treating Process
- Heating: The metal is heated to a specific temperature, depending on its composition and the desired outcome. This step helps to realign the atomic structure of the metal.
- Soaking: Once the metal reaches the target temperature, it is held there for a set amount of time. This ensures uniformity in the structural changes.
- Cooling: The metal is then cooled at a controlled rate. The cooling medium—air, oil, or water—determines the final properties of the metal.
Understanding these steps highlights how the heat treating process creates a material tailored to specific applications, ensuring improved metal durability and performance.
How Heat Treating Enhances Metal Durability
Metal durability is essential for components that endure heavy loads, repeated impacts, or harsh environments. The heat treating process significantly improves this characteristic in the following ways:
Refining the Grain Structure
Heat treating modifies the grain structure of metal, making it finer and more uniform. This grain refinement reduces the likelihood of cracks and improves resistance to fatigue. For example, quenching and tempering steel produces a robust microstructure, enhancing its load-bearing capacity.
Increasing Hardness
Hardness is a critical factor in determining a metal’s resistance to deformation. Processes like case hardening create a hard outer layer while maintaining a tough core. This combination is particularly valuable for gears, tools, and other components exposed to high friction.
Improving Wear Resistance
Wear resistance is crucial for components subjected to abrasion or erosion. Through heat treating, metals achieve a surface hardness that reduces wear, extending the life of parts used in machinery and industrial equipment.
Reducing Residual Stresses
Residual stresses can weaken a metal’s structural integrity, making it more prone to failure. Annealing and stress-relief heat treatments reduce these stresses, ensuring the material maintains its strength over time.
Boosting Performance with Heat Treating
Beyond durability, the heat treating process also optimizes metal performance by tailoring its properties to meet specific operational demands.
Enhancing Toughness
Toughness is the ability of a metal to absorb energy and resist fracture. By controlling the cooling rate during heat treating, manufacturers can balance hardness and toughness, producing materials that perform well under impact.
Increasing Ductility
Certain applications require metals to be ductile, allowing them to stretch without breaking. Heat treating techniques like annealing enhance ductility, making metals easier to form and shape for intricate designs.
Customizing Strength-to-Weight Ratio
The strength-to-weight ratio is a critical factor in industries such as aerospace and automotive, where reducing weight without sacrificing strength is paramount. Heat treating aluminum alloys, for instance, achieves this balance, enabling lightweight yet strong components.
Enhancing Corrosion Resistance
Corrosion is a major challenge for metals exposed to moisture, chemicals, or extreme environments. Heat treating can improve corrosion resistance, particularly in stainless steel, by enhancing its protective oxide layer.
Types of Heat Treating Processes
Different heat treating methods are employed to achieve specific improvements in metal durability and performance. Here are the most common processes:
Annealing
Annealing involves heating metal to a specific temperature and then cooling it slowly. This process relieves internal stresses, improves ductility, and refines the grain structure, making the material easier to work with.
Quenching
Quenching rapidly cools heated metal, typically using water, oil, or air. This process increases hardness and strength but may reduce toughness if not followed by tempering.
Tempering
Tempering is often performed after quenching to reduce brittleness while retaining hardness. The metal is reheated to a lower temperature and then cooled, achieving a balance of strength and toughness.
Case Hardening
Case hardening involves hardening the outer surface of a metal component while keeping the core ductile. Techniques like carburizing and nitriding are common in this category, ideal for components like gears and bearings.
Normalizing
Normalizing heats metal to a high temperature and allows it to cool in air. This process refines the grain structure, improving mechanical properties and ensuring uniformity.
Applications of Heat Treated Metals
The benefits of the heat treating process make it indispensable across various industries. Let’s explore some key applications:
Aerospace
In the aerospace sector, lightweight and durable materials are essential. Heat treating aluminum alloys ensures high strength-to-weight ratios, while processes like precipitation hardening enhance fatigue resistance.
Automotive
Heat treated metals are crucial in manufacturing engine components, gears, and suspension systems. The process ensures these parts can withstand high stresses and wear.
Manufacturing Tools
Cutting tools, molds, and dies require exceptional hardness and wear resistance. Heat treating delivers the properties necessary for these tools to perform reliably in high-pressure environments.
Construction
Structural steel used in buildings and bridges benefits from heat treating, which enhances its strength and ability to bear heavy loads over extended periods.
Energy Sector
Heat treated metals play a vital role in power plants, pipelines, and renewable energy systems. Their enhanced durability and performance ensure reliability in extreme conditions.
Factors Influencing Heat Treating Outcomes
While the heat treating process is highly effective, its success depends on several factors:
- Metal Composition: The alloy’s chemical makeup determines its heat treating response and achievable properties.
- Temperature Control: Precise temperature management is critical to avoid defects or uneven properties.
- Cooling Medium: The choice of cooling medium affects the rate of cooling and, consequently, the final properties of the metal.
- Time Duration: Both soaking and cooling times must be carefully controlled to achieve the desired results.
- Equipment Quality: Advanced furnaces and monitoring systems ensure uniform heating and cooling, producing consistent outcomes.
Advancements in Heat Treating Technology
Recent innovations in the heat treating process have further enhanced its capabilities, enabling greater control and efficiency:
Induction Heating
Induction heating uses electromagnetic fields to heat metals selectively. This method is faster and more energy-efficient, ideal for localized heat treating.
Vacuum Heat Treating
Vacuum heat treating eliminates oxidation by conducting the process in a controlled vacuum environment. This ensures cleaner and more precise results.
Computerized Controls
Modern heat treating facilities use computerized systems to monitor and control every aspect of the process, ensuring consistency and reducing human error.
Conclusion
The heat treating process is a cornerstone of metalworking, offering unparalleled improvements in metal durability and performance. By refining grain structures, enhancing hardness, and optimizing mechanical properties, heat treating ensures metals can meet the demands of diverse applications. From aerospace and automotive to construction and manufacturing, industries rely on heat treated metals to deliver strength, reliability, and longevity. As technology continues to advance, the potential for heat treating to revolutionize metalworking grows, paving the way for even greater innovations in durability and performance.
Need Heat Treatment Services in Gastonia, NC?
Family owned and operated J.F. Heat Treating Inc, is a metal heat treating service company with more than 34 years of experience! Heat treatment is the controlled heating and cooling of metals to alter their physical and mechanical properties without changing the product shape. We specialize in the through hardening and carbonizing of various steel products in a metallurgical lab. It is our privilege to service and work with the manufacturing and fabrication industries to give the best product service available! Our heat treating services include annealing, aging, quenching and tempering to soften, harden, stress relieve, remove contaminants or provide other material characteristics to parts and components. Contact us today to learn more about what we can do for you!