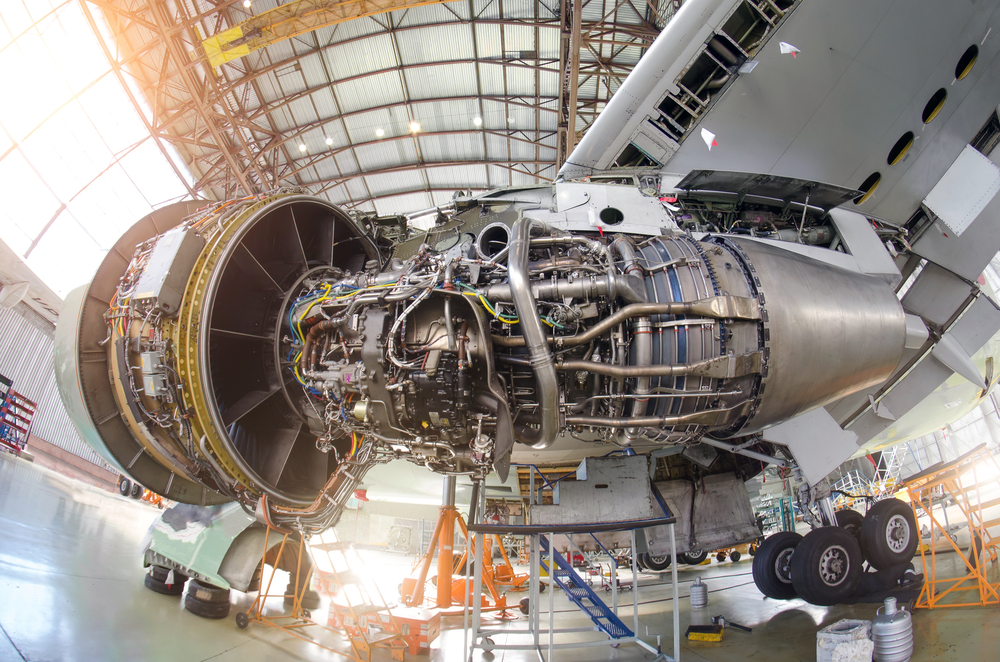
Heat treatment is a critical process in the manufacturing of aerospace components, playing a pivotal role in enhancing their mechanical properties, durability, and overall performance. Aerospace engineers and manufacturers rely heavily on heat treatment techniques to achieve specific material characteristics required for safety, reliability, and efficiency in aircraft and spacecraft operations. This blog explores the importance of heat treatment in aerospace, detailing its processes, benefits, and the impact on component performance.
What is Heat Treatment?
Heat treatment involves heating and cooling metals or alloys in a controlled manner to alter their physical and mechanical properties. The process aims to optimize characteristics such as hardness, toughness, strength, and ductility to meet stringent aerospace requirements. Different heat treatment methods, including annealing, quenching, tempering, and solution treatment, are employed based on the material type and desired properties.
Importance in Aerospace Applications
In aerospace, where components are subjected to extreme conditions of temperature, pressure, and mechanical stress, the reliability and durability of materials are paramount. Heat treatment ensures that materials used in critical components, such as turbine blades, landing gears, and structural elements, possess the necessary strength to withstand these conditions without failure or deformation.
Benefits of Heat Treatment in Aerospace Components
Enhanced Strength and Hardness
One of the primary benefits of heat treatment is the enhancement of material strength and hardness. Through processes like quenching and tempering, aerospace components can achieve high tensile and yield strength, crucial for withstanding dynamic loads during flight and ensuring structural integrity under stress.
Improved Wear and Corrosion Resistance
Heat treatment also improves the wear and corrosion resistance of aerospace components. By modifying the microstructure of materials, heat treatment reduces susceptibility to surface damage and degradation caused by friction, erosion, and exposure to environmental factors such as moisture and chemicals.
Precise Control Over Material Properties
Aerospace materials must meet exacting standards for performance and reliability. Heat treatment provides engineers with precise control over material properties, allowing them to tailor hardness, toughness, and other characteristics to meet specific operational requirements. This customization is essential for optimizing the weight-to-strength ratio of components and minimizing the risk of premature failure.
Impact on Aerospace Component Performance
Durability and Fatigue Resistance
Heat-treated aerospace components exhibit improved durability and fatigue resistance compared to untreated materials. The process refines the grain structure of metals, reducing internal stresses and susceptibility to fatigue cracking, which is critical for components subjected to cyclic loading during flight cycles.
Dimensional Stability
Aerospace components often operate in environments where temperature variations are significant. Heat treatment minimizes dimensional changes in materials due to thermal expansion and contraction, ensuring dimensional stability over a wide range of operating temperatures. This stability is vital for maintaining precise fit and alignment of critical parts within the aircraft or spacecraft.
Consistency and Reliability
Consistency in material properties is essential for the reliable performance of aerospace components. Heat treatment processes are standardized and meticulously controlled to ensure uniformity across batches of materials. This consistency minimizes variability in component behavior, contributing to overall reliability and safety in aerospace applications.
Innovations in Heat Treatment Technology
Advanced Techniques
As aerospace engineering continues to advance, so too does heat treatment technology. Innovations such as induction heating, rapid quenching methods, and computer-controlled heat treatment cycles enable more precise control over material properties while reducing processing times and energy consumption. These advancements contribute to efficiency gains in manufacturing and enhanced performance in aerospace components.
Simulation and Modeling
Modern computational tools allow engineers to simulate heat treatment processes and predict material behavior accurately. Finite element analysis (FEA) and computational fluid dynamics (CFD) simulations help optimize heat treatment parameters, ensuring that aerospace components achieve desired properties while minimizing material waste and production costs.
Conclusion
Heat treatment is indispensable in the aerospace industry, ensuring that materials used in critical components meet stringent performance requirements for safety, reliability, and efficiency. By enhancing strength, durability, and dimensional stability while improving wear and corrosion resistance, heat treatment processes play a vital role in shaping the performance and longevity of aerospace components. As technology evolves, so too will heat treatment methods, continuing to support the innovation and advancement of aerospace engineering.
Need Metal Tempering Services in Charlotte, NC?
Family owned and operated J.F. Heat Treating Inc, is a metal heat treating service company with more than 34 years of experience! Heat treatment is the controlled heating and cooling of metals to alter their physical and mechanical properties without changing the product shape. We specialize in the through hardening and carbonizing of various steel products in a metallurgical lab. It is our privilege to service and work with the manufacturing and fabrication industries to give the best product service available! Our heat treating services include annealing, aging, quenching and tempering to soften, harden, stress relieve, remove contaminants or provide other material characteristics to parts and components. Contact us today to learn more about what we can do for you!